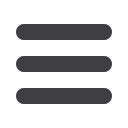
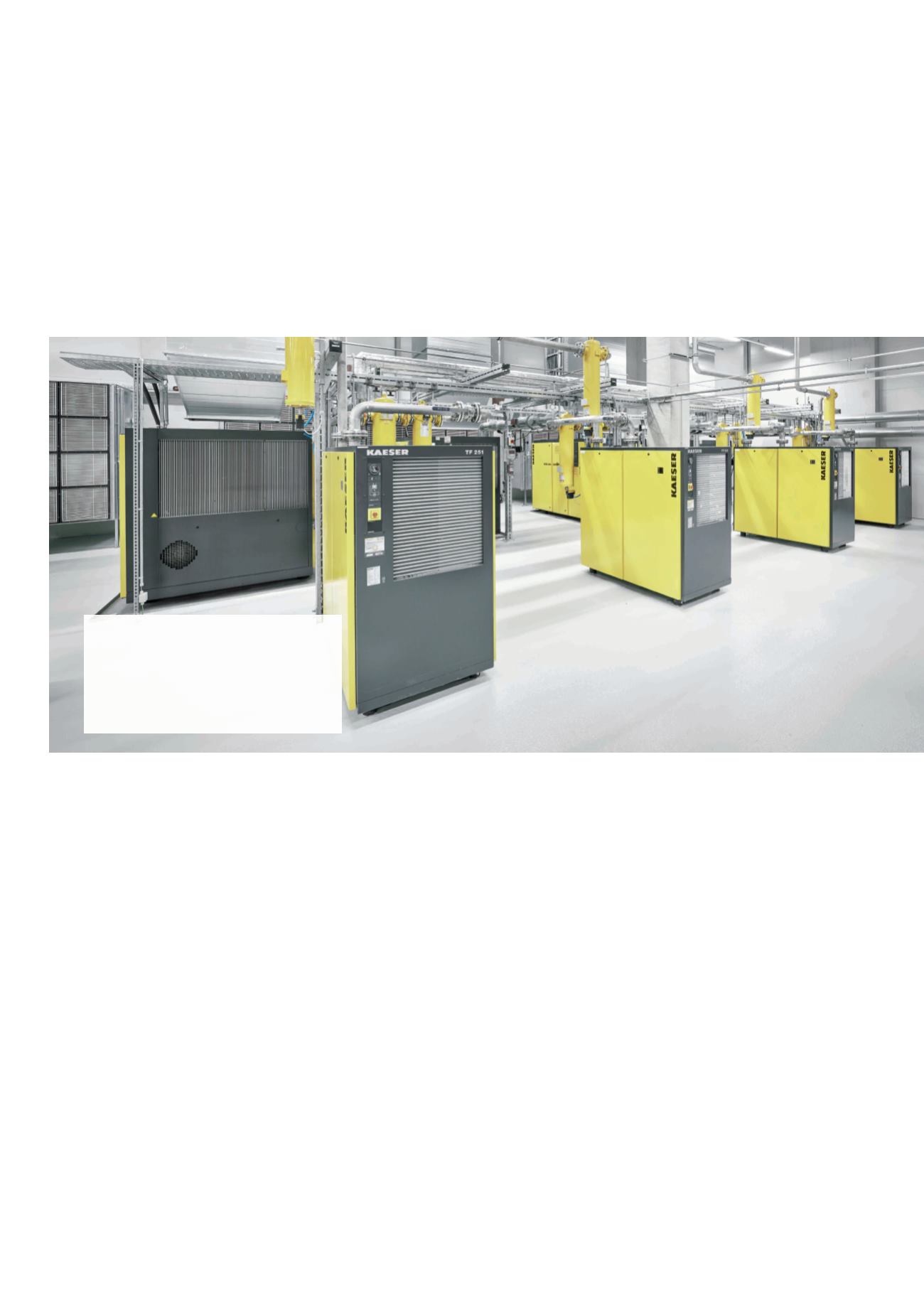
Festo AG & Co KG
01 Emanating from the central com-
pressed air system, the whole factory is
supplied with compressed air via differ-
ent networks
01
Environmental targets
• Sustainable and ecologically viable operations
• Forerunner in terms of energy efficiency
• One per cent annual improvement in the key
energy figures
Components are electrolytically treated
there and thus made resistant to corrosion
or given particular surface properties
Instead of outsourcing it, the planners
made the conscious decision to integrate
this costly procedure
Products and components are expected to
pass through the factory as quickly as pos-
sible whilst conserving as many resources
as possible Sophisticated insulation on
the electroplating tank today saves around
15,000 cubic metres of exhaust air each
hour Furthermore, the ventilation system
is equipped with a heat exchanger to
recover energy The waste heat from the
combined heat and power stations is used
to heat water
The generation of compressed air repre-
sents another major consumer of energy
Centre for building services
All the supply facilities – combined heat
and power stations, boilers, cooling
machines, distributors, pumping stations,
cooling towers and the central compressed
air system – are housed in a separate
building on the premises Heat, cold, cool-
ing water and compressed air are fed from
this technical centre to the production lev-
els via an accessible media duct Pipe
routes, which are arranged at an interval
of nine metres, and can be accessed every
three metres, make up a continuous sup-
ply network Production equipment can be
flexibly rearranged at any time, without
changes being necessary to the building
infrastructure The structure also provides
every possibility for a further expansion of
the Technology Plant if required
Data volumes under control
To safely operate the equipment in the
buildings, all consumption data and the
correct function of the individual facilities
are continually recorded The data comes
together in a central building management
system The facilities are automatically
controlled from here Thanks to the clear
visualisation system, any faults can be dis-
played in real time on a computer or tablet
and action taken if necessary By prioritis-
ing the types of alarm, the emergency ser-
vices can estimate whether they are
needed on-site – at night, for instance
Keeping an eye on large facilities
The planners paid special attention to the
large facilities from the start In the Tech-
nology Plant, electroplating is the single
facility that consumes the most energy
20