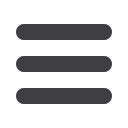

01 Material is transported in the Tech-
nology Plant with pinpoint accuracy via
synchronised tugger trains.
Scharnhausen Technology Plant: Flowing production
duction chain is much shorter transporta-
tion routes for delivering, sawing, machin-
ing, deburring, cleaning and electroplating
components. Whilst the process used to be
distributed across several plants over a dis-
tance of 32 kilometres, they were able to
be reproduced across just 120 metres in‑
side the Technology Plant.
Logistics performance
In the lean Technology Plant, material flows
through the production halls like blood
through arteries and veins. The individual
manufacturing processes are combined
with each other by the shortest of routes
and arranged so that, as far as possible,
there is need for interim buffering across
warehouse stocks. So-called tugger trains
ensure the smooth flow of materials
between production and logistics. These
are small electric vehicles with trailers,
which stop at defined points in the produc-
tion department in a fixed cycle like service
buses. The transfer points are uniformly
marked throughout the plant so that it can
be immediately seen where and which
goods have to be dropped off or picked up.
No bottleneck
Any process chain overall can only be as
strong as its weakest link nevertheless. In
order to prevent bottlenecks, the factory
experts apply the Theory of Constraints of
the physicist, Eliyahu Goldratt. Instead of
improving each partial process individu-
ally, the focus should be on the bottleneck
according to Goldratt. The bottleneck is
specifically optimised and the process
steps before it only feed it the amount of
material that can be processed. In this
way, an optimal result can be achieved for
the whole factory.
Setting standards
Suppliers are also firmly integrated in the
factory processes. They are responsible
themselves for delivering materials accord-
ing to defined inventory limits. Their link is
established, whenever possible, by means
of standardised and cyclically synchro-
nised delivery vehicles. Besides material
logistics, there are numerous standards for
work materials, among other things.
Employees select their own office supplies
or tools from a standard work system. In
order to ensure the adaptability in future
too, today’s standards are constantly being
developed as part of the Festo production
system Festo Value Production (FVP).
01
9