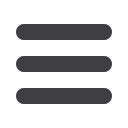
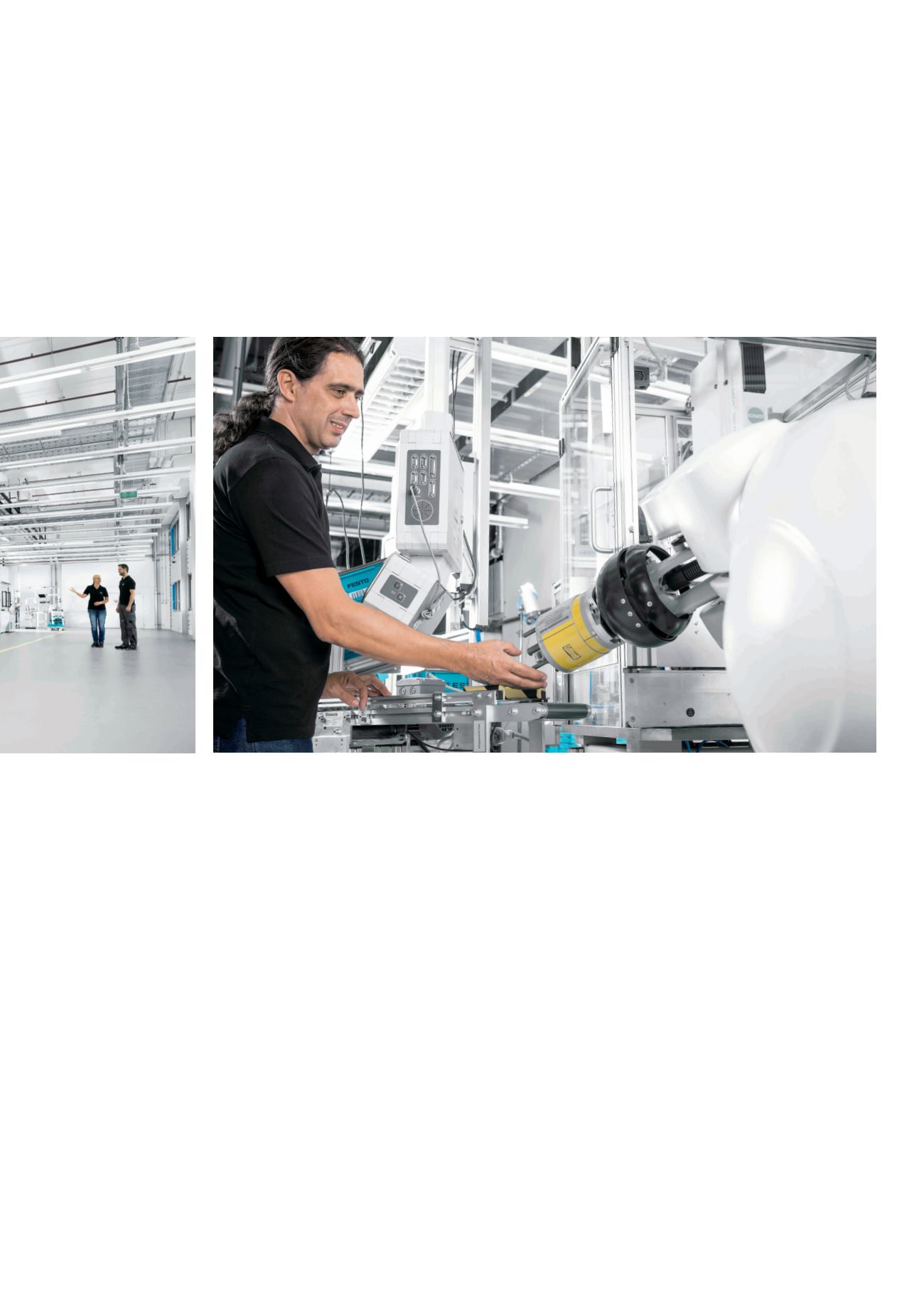
Scharnhausen Technology Plant: Automated and adaptable
01 Valves are automatically assembled
in the production cells of the large modu-
lar lines
02 An employee works with the
assembly robot in an intuitive and risk-
free manner.
02
Everything can be tracked
Right from the planning stage, the experts
ensured a high energy-efficiency level on
the assembly lines. The energy consump-
tion can now be individually determined
for each unit today. Possible leaks are auto-
matically detected, whilst pressure and
flow rate are continually monitored. Locally
employed valve terminals reduce the con-
sumption of compressed air on the ma‑
chines considerably. Thanks to cameras and
laser sensors, each separate assembly
step is inspected without delay. Barcodes
and RFID chips (radio frequency identifica-
tion) are used across the entire production
process and beyond, from the supplier to
the customer, to record batch data, process
parameters and all test results. Unfavoura-
ble trends in production can thus be identi-
fied early on, and waste or reworks avoided.
Human-robot cooperation
The adaptability of the automation process
combined with an intuitive human-machine
interface and the qualification of employ-
ees make up key aspects of the production
of tomorrow. Special machines or a robot
thus take over pre-assembly jobs, which are
ergonomically one-sided for people or have
a very short cycle. The robot grips a hous-
ing, joins cartridges and frame together and
ultimately passes the component on to the
worker for further processing. Such team-
work poses no risk for the person. Sensors
monitor all the robot’s actions. As soon as
an employee comes too close to it, the
robot slows down or just stops. Thanks to
safety mechanisms, the robot does not
have to be behind bars: a successful exam-
ple for the future-oriented and competitive
partnership between man and machine.
13