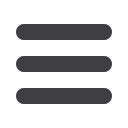
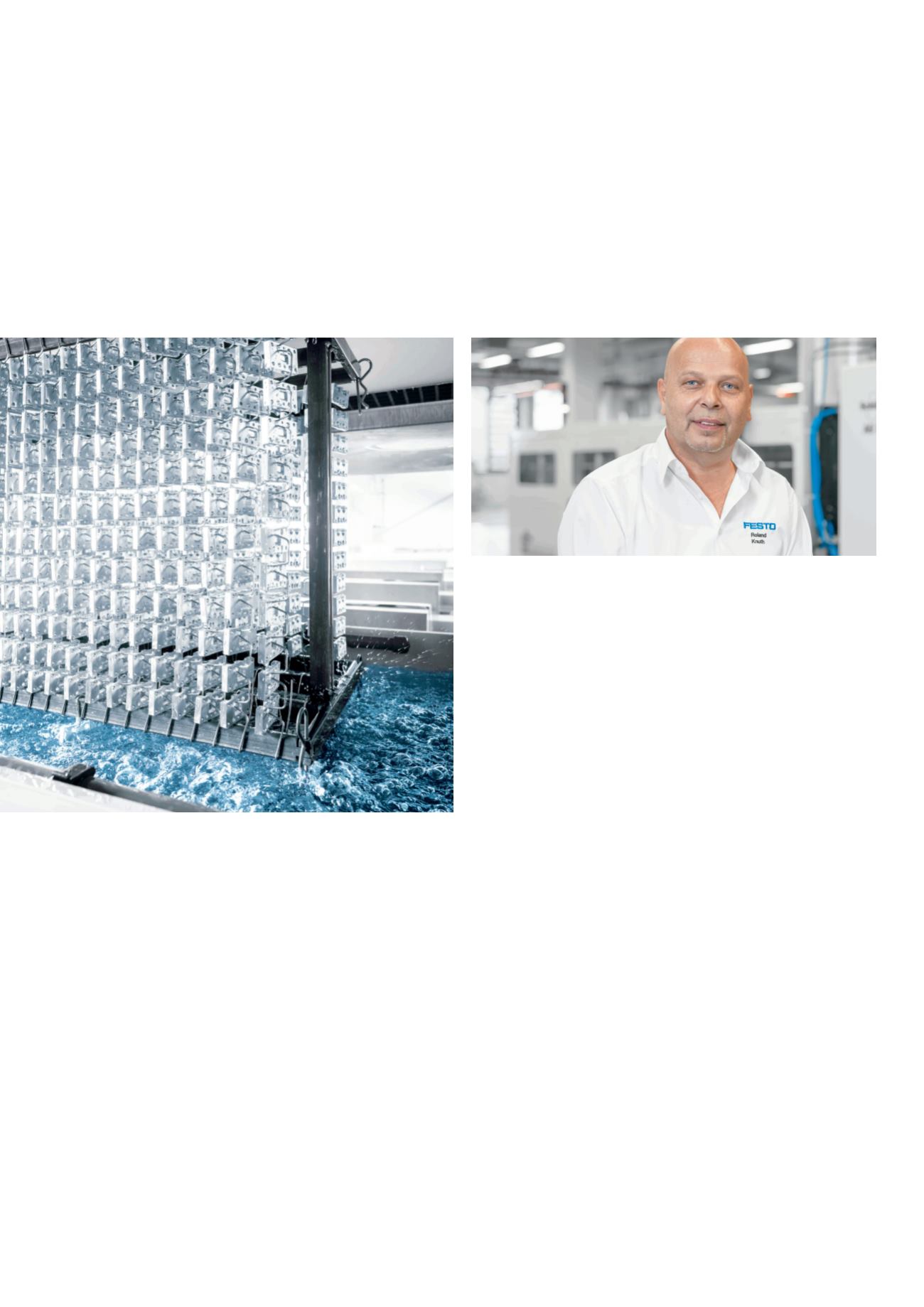
11
Scharnhausen Technology Plant: Perfect in form
02 The components’ surfaces
are enhanced in the electroplating
department.
01 The machine inserts seals in the
pre-produced valve cartridges.
Safe, clean and efficient
Metal-cutting facilities require a lot of energy due to the effort
needed when machining metal. Machines and ancillary units were
therefore efficiently designed from the start using innovative tech-
nology. As soon as they are idle, they switch to a suitable ener-
gy-saving mode that takes start-up times, product quality and
safety into account. The functionality of the machines and the
product quality are continually checked and ensured. The worksta-
tions of the specialists for maintenance and test procedures are
therefore located in the middle on the machining department level,
where they are most needed.
The mechanical metal machining results in chips and exhaust air
containing oil. An ultra-modern extraction unit is used to filter the
air and recover heat. Even the finest particles are therefore unable
to get into the air in the factory. The chips created are collected,
pressed into briquettes and resold as aluminium scrap.
»I startedmy training at Festo 33 years ago. Our machines
in the Technology Plant produce the cartridge sleeves
in a matter of seconds. We develop the special tools
that are needed for this ourselves.«
Plating and pickling
The components are immersed in plating tanks to give them the
necessary surface properties using electrolysis. The washed
and degreased aluminium parts from the machining department
are firstly pickled, whereby a layer of about ten micrometres
is removed. In the anodising process they are finally given a
20 micrometre thick coating, which protects them from corrosion
and ensures a low-friction surface. The plating process at the Tech-
nology Plant is energy efficient. Several components can thus be
anodised simultaneously in one tank and no retooling is necessary
to change the anodising substances. A heat exchanger allows
energy to be recovered from the ventilation system.
Roland Knuth, Head of Valve Cartridge Production
02