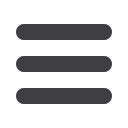
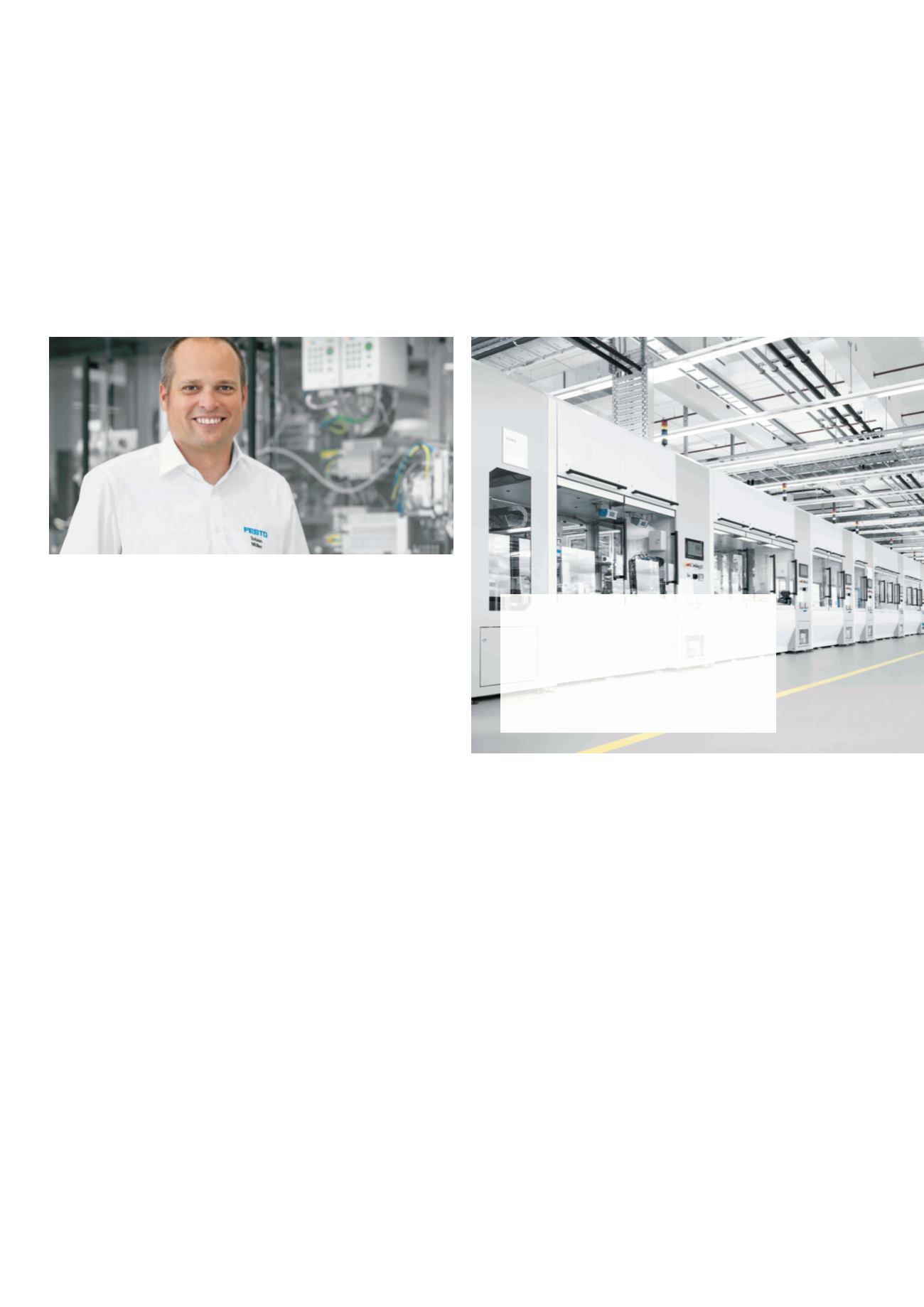
Festo AG & Co KG
Automated and adaptable
Products are manufactured in a very short space of time
on highly flexible and energy-efficient assembly lines
01
A wide range of solenoid valves and valve
terminals are produced automatically or
even manually in the assembly depart-
ment Many of the company’s own products
and applications provide support here:
Festo products are used to manufacture
Festo products For example, small, com-
pact solenoid valves are automatically
assembled on the latest assembly lines
The lines each produce over 50 individual
variations of different sizes, whereby 20
variations make up over 80 per cent of the
total volume When it comes to assembling
the valves to make valve terminals, manual
work is still required An enormous product
variety of 10 40 types – a number one with
40 zeros – is possible in the case of many
products, which have to be made according
to individual customer specifications in a
very short space of time
Cell by cell
In the assembly lines there are up to eight
production cells spread one after the other
over 30 metres; this is where the motion
sequences for assembling the individual
valves are controlled and executed
This includes spray greasing the housings,
pressing in the cartridges and fitting the
seals, as well as ensuring the respective
process monitoring procedures
The specialists for automation created the
cells both in the hardware and the software
with a modular design and networked them
with each other The individual processes
are autonomously set up, whilst the cells’
interfaces are standardised It is possible
to convert, replace or extend the cells with-
out a great deal of effort A time slot no
longer has to be planned even for retool-
ing, as the system retools itself within the
cycle time The consistent standardisation
process means that even assembly cells or
modules made by other manufacturers can
be integrated as required
Correct greasing
To grease the pistons, the Festo experts
use a clever method in the automated
assembly process: special grease is finely
atomised by a heatable spraying system
and applied safely and accurately using
spray nozzles The process data for this
production step is constantly monitored In
service life tests, the solenoid valves thus
perform five times better than before.
For testing the valves after the last produc-
tion step, an innovative test system has
been developed, by which it has been pos-
sible to reduce the time required for this to
just a few seconds
»We ensure the quality and availability of the automated
assembly facilities In the morning we get together for
a short, standardised coordination meeting Our aim is
not only to rectify problems but to analyse them in a
proactive way Especially when assembling large quan-
tities, we want to identify critical process values early
enough so that we can react before a fault occurs «
Tobias Müller, Head of Assembly Work Preparation
Fully automated valve assembly
• Two production lines for solenoid valves
• Several million fully automatically assembled valves
per year
• Assembly and testing completed in a few seconds
• Exceptional flexibility and variation
12